Photos by Sue Barr and AA students
Designers: AA students
Location: Architectural Association, Bedford Square, London
London’s Bedford Square is once again being transformed by the arrival of a dynamic timber structure. The Swoosh is this year’s winner of the AA’s summer pavilion competition.
Working from an original concept by student Valeria Garcia, 12 second- and third-year students, supervised by tutors Charles Walker and Martin Self, have collaborated over 30 weeks to transform a 2D drawing and a towering pile of timber into a thoughtful and aesthetically forceful space.
This year’s judges included BD’s editor Amanda Baillieu, Renato Benedetti of McDowell & Benedetti Architects, Alex de Rijke of dRMM, Warren Dudding of Finnforest and Ian Fleetwood of HOK.
Walker and Self say they gave a very open brief. “We asked them to create a pavilion for 100 people with some level of enclosure, and that was basically it,” says Self. The response is a swirling, 60m-wide pavilion which wraps itself around a sturdy lamppost and skirts the pavement enclosing Bedford Square’s central green. It is made of 653 pieces of timber and consists of vertical curving columns — connected by hundreds of short beams — spiralling out from a central fulcrum. While the centre is dense and enclosed, the tails of the spiral taper out to become benches.
“We wanted to create an interactive space where people could share different experiences, like holding informal meetings, sitting, having lunch — all under one roof,” says student Eyal Shaviv.
As for the form, fluidity was the driving factor. “The main goal was to create a sense of flow,” says student Katrina Scoufaridou. “We have used many vertical pieces, but because they are connected to form a grid, the whole structure has a sense of cohesion.”
Sunshine through the lattice creates a shadow of the 2D pattern that the students started with. The pavilion’s complex geometry meant they had to switch from a computing scripting model to handcrafted 3D models, calculating many details by themselves.
“They realised they couldn’t just sit back and press a button, and the computer would do it all for them,” says Self.
Their collaboration with Arup also led to the height of the pavilion rising from 2.5m to 3.3m, which ultimately produced a more elegant solution. “It’s great for the students to experience the seeds of the idea germinating and growing into a realised project,” Self adds.
The Timber

The structure is made almost entirely out of Kerto, a laminated veneer lumber donated by Finnforest. The students specified sheets 27mm thick for the beams and 51mm thick for the columns.
“We decided to use different timber thicknesses for the beams and columns early on, because we thought it would add a further detail and add grace to the pavilion,” says Eyal Shaviv.
Students cut 549 beams from the 27mm sheets using a CNC machine. Since the 62 columns were too large to cut from one 51mm sheet, many were formed out of two or three separate pieces.
The design uses a lot of material, which inevitably led to a mountain of offcuts. Some of these have been ingeniously recycled to create tools such as a trolley and the library stands that stored batches of beams.
“Because there are so many separate pieces, we had to be very vigilant in labelling, separating and storing them all,” says Shaviv.
The Plan
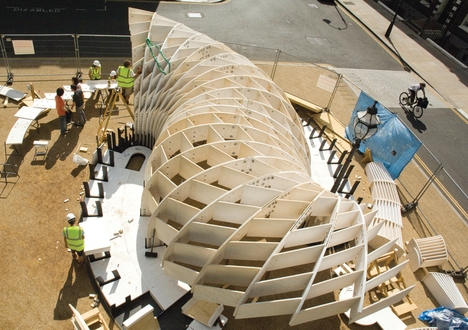
Software programs Rhino and Autocad were used to design the original concept: Autocad mainly for measurements and labelling, and Rhino for quicker modelling and 3D visualisation.
The plan is devised around two setting points, A and B, and two identical columns, A01 and B01, which run between the two. From the setting points, 30 more columns spiral outwards in each direction, creating a completely symmetrical form. Columns A01 and B01 form an archway, 3.3m in height. The remaining columns then get taller as they cantilever out to create a partly enclosed space.
At column B17 and A17, the pavilion reaches its highest point of 4.5m. From here, the beams reduce in height, eventually reconnecting with the floor to create benches at the tail end of each spiral. Ten equally spaced beams run in the voids between the columns, with the spacing becoming increasingly dense as the length of the columns reduce.
“The beams get closer and closer together until eventually they are close enough to form a comfortable seat at the ends,” says Katrina Scoufaridou.
Staining
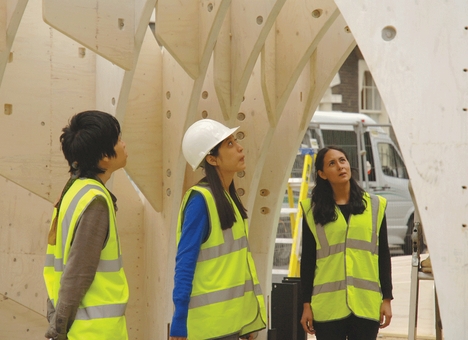
A white, almost transparent stain was used to give the pavilion a lighter appearance. “It’s not a heavy structure, but there’s a lot of material. We thought this colour would help with fluidity and prevent it from feeling oppressive,” says Shaviv.
Two types of stain have been used. The first is Osmo, an environmentally friendly German product that has no biocides or preservatives and only uses aliphatic, a low-odour mineral spirit. The second, required when not enough Osmo was ordered, is from Sadolin.
“The difference is not very noticeable. Once the structure is complete, it will create subtle differences in shading,” says Shaviv.
One coat was applied to the vertical pieces, and a further coat has been applied to the horizontal stage and seating areas as these are more exposed to the rain.
Connections
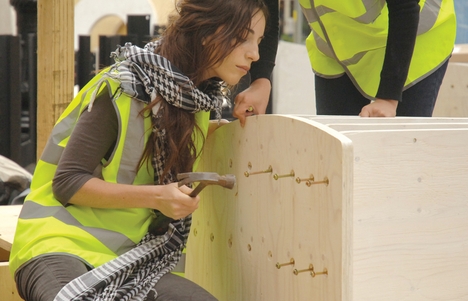
A variety of bolts connect the beams and columns, although most are M12 hexagonal. The students decided to use bolts rather than screws so the structure could be more easily dismantled and rebuilt.
“The easiest solution would have been to drill straight through,” says Shaviv. “Instead, we created pockets for the bolts with pre-cut holes. This way, you can reuse the bolt and you don’t cause any damage or weaken the structure. With screws, reassembling would have been a problem.”
The columns are also strengthened at their centre with steel plates that slot into pre-cut voids and are then bolted into position.
Arranging the Beams and Columns
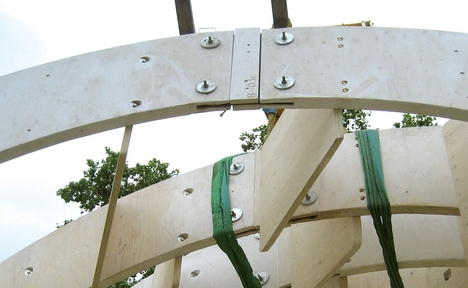
Each beam and column has been carefully labelled to correlate with the plan. For example, beam A-12-T05 corresponds to column A-12, and is slotted between beam A-12-T04 and A-12-T06. The labels, cut into the timber surfaces, have been clearly left on display.
“It’s part of the detailing and tells the story of the structure,” says Scoufaridou. “It also means the pavilion can be easily dismantled, stored and rebuilt.”
The Base
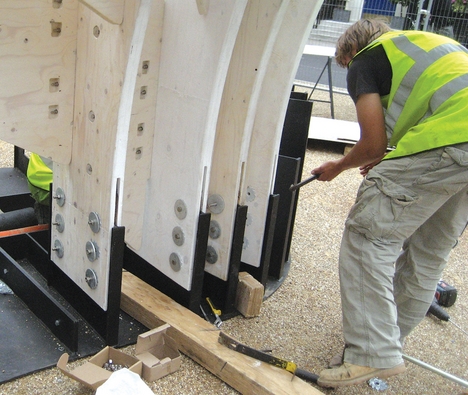
The structure sits on two steel bases, each made up of four interconnected parts, which are prefabricated and coated with black primer by manufacturer Sheetfabs.
The students designed the base to weigh over 6 tonnes in order to secure the cantilevered columns. The pavilion will be lifted on to the carefully positioned base once it has been built.
Vertical steel sheets slot into pre-cut voids at the base of each column and are bolted to set the steel ends flush against the timber. This is the only visible evidence of the base as the steel floor is covered by a timber stage and seating.
Only five sections are not connected to the base — those at the end of each tail, which act as benches. These don’t require additional support; each bench is being made individually and bolted together.
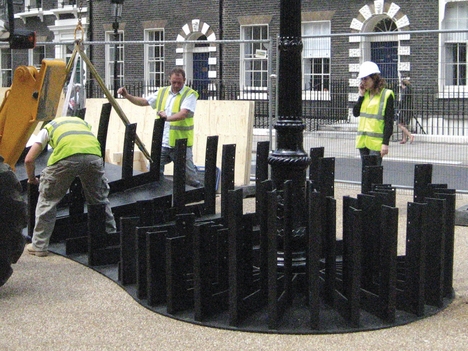
'Pavilion&Installation' 카테고리의 다른 글
[Maya Lin] Systematic Landscapes (0) | 2008.07.10 |
---|---|
[Cadaval & Solà-Morales] Susana Solano exhibition (0) | 2008.07.07 |
[Arne Quinze] Rebirth (0) | 2008.07.07 |
[Zaha Hadid] Zaragoza Bridge Pavilion (0) | 2008.07.03 |
[ Maya Lin ] Bronze Glory (0) | 2008.06.29 |